As a near-net forming technology, die casting is widely used in industries such as automobiles, aerospace and communications due to its high production efficiency and good casting quality. The performance of die castings is mainly affected by its microstructure. As a kind of microstructure, a defect is one of the most common but most influential factors.
There are many types of defects in
die castings, but they can be roughly divided into the following three categories according to the process flow: The first category is related to the flow process, that is, the defects that may occur in the filling process, including
gas entrainment, oxide layer entrainment (also called inclusions) and flow marks. The second one has relevance to the solidification process, including shrinkage cavity and shrinkage porosity. The third category is related to the heat treatment process after taking out die castings, including thermal deformation and defect aging. However, this article focuses on the common gas entrainment and inclusion defects in the die casting filling process.
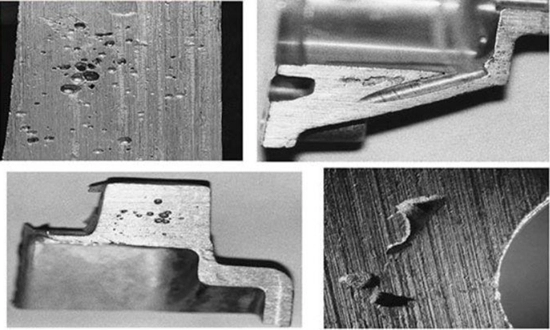
Figure 1. The gas hole defect of typical castings
Causes
Different from ordinary casting process, the greatest feature of die casting is high speed and high pressure. High speed refers to the very high speed of the die casting filling process, and the inner gate speed can often reach 30m/s to 60m/s; in some cases it is even higher. High pressure means that the solidification process of die casting is completed under very high pressure. After the filling of die casting is completed, pressurization is often used to increase the casting pressure with tens to hundreds of megapascals, depending on types of die castings and models of die casting machines and capacity of hydraulic equipment. Enhance the internal liquid feeding of the casting and improve the heat transfer efficiency of the casting-mold interface.
In the filling process, the liquid metal is often splashed due to the extremely high flow speed, and even in most cases, atomization occurs at the position of the inner gate. At this time, the liquid tends to roll over, so it cause gas entrainment inside the liquid. This kind of
gas entrainment is actually the liquid flow at the confluence which wrap the air inside the liquid and then flow with the liquid.
Generally speaking, the air mass wrapped in the liquid will be broken under the flushing of the liquid, or will polymerize with other air masses as the liquid flows to form larger air masses. We may intuitively feel that if the liquid filling speed is extremely low, then the surface of the liquid will be very stable in the filling process; no gas entrainment will occur. As a matter of fact, if the filling speed is extremely low, the filling time will become longer. It is very likely that the liquid has solidified before it is completely filled into the cavity, resulting in insufficient pouring. Therefore, in actual applications, this slow filling can only be used if the casting structure itself is relatively thick and big. This process is also called ultra-low speed filling.
If the mold design is improper, especially when the exhaust channel is not smooth, the liquid metal will form another kind of gas entrainment due to the back pressure in the filling process. The so-called back pressure is the air mass formed under the force of the molten metal because the residual gas in the cavity cannot be discharged. It usually formed at the last position of the filling. Compared with the gas entrainment in the filling process, the volume of the air mass caused by the back pressure is larger and the damage is more serious. Therefore, in the process of mold design, the exhaust channel should be designed reasonably to avoid this kind of gas entrainment caused by back pressure.
There is another defect called oxidation
inclusions in the filling process. Liquid metal which is in contact with air will generally form an oxide layer with thickness of nanometers to micrometers on the surface. This oxide layer will be wrapped from surfaces to the inside of liquid with the flow of liquid to form the so-called inclusions.
In the die casting process, this inclusion is generally divided into two types: The first is the oxide layer formed by the liquid metal in the smelting process. This oxide layer will be wrapped into the metal with the subsequent flow of the liquid metal; the second type is an oxide layer formed by oxidizing the metal surface inside the cavity in the filling process of liquid metal.
Figure 2. SEM morphology characterization of the aluminum alloy double oxide film and EDS composition characterization
In the cold chamber die casting process, the molten metal from the smelting furnace is first poured into the pressure chamber. The high-temperature liquid metal will form a dense oxide film on the surface due to rapid oxidation, and this oxide film will also be filled when the molten metal enters the cavity and becomes a potential source of
inclusions. Compared with the oxide film formed on the surface of the molten metal in the cavity, once the oxide formed in the melting process and the pressure chamber is cased in the inner part of castings, it will have a greater impact on the performance of the casting.